erp productie sets the stage for this enthralling narrative, offering readers a glimpse into a story that is rich in detail and transformative for the manufacturing sector. As industries strive for increased efficiency and productivity, the integration of Enterprise Resource Planning (ERP) systems into production processes has become essential. This discussion will delve into the significance of ERP production, exploring its core components, implementation strategies, key features, and the future trends that are shaping its trajectory.
Understanding ERP production is crucial for manufacturers seeking to streamline operations and maintain a competitive edge. By leveraging ERP systems, organizations can optimize their production workflows, enhance real-time data utilization, and ultimately drive greater profitability. This comprehensive overview will illuminate how ERP production not only supports operational needs but also fosters innovation in the manufacturing landscape.
ERP Production Overview
ERP production refers to the integration of Enterprise Resource Planning (ERP) systems within manufacturing processes to streamline operations, enhance productivity, and improve overall efficiency. This approach allows organizations to manage their resources, production schedules, supply chains, and inventory levels cohesively. The significance of ERP production in manufacturing cannot be overstated, as it empowers businesses to adapt swiftly to market demands while maintaining optimal resource utilization.The core components of ERP systems in production encompass various functions that collectively contribute to improved operational performance.
These components typically include modules for production planning, inventory management, procurement, quality control, and human resources. Each module plays a crucial role in ensuring that all aspects of the production process are harmonized. For instance, production planning modules help determine the most efficient workflows and resource allocation, while inventory management modules provide real-time visibility into stock levels, thus minimizing waste and ensuring timely availability of materials.
Core Components and Functions of ERP Systems in Production
The integration of ERP systems in production involves several vital components that work together to enhance efficiency and visibility. These components are instrumental in facilitating informed decision-making and optimizing production processes.
- Production Planning: This module assists in forecasting demand, scheduling production runs, and managing capacity. By analyzing historical data and market trends, businesses can create accurate production plans that align with demand.
- Inventory Management: Effective inventory management is crucial for maintaining optimal stock levels and avoiding shortages. ERP systems provide real-time tracking of inventory, helping manufacturers replenish supplies as needed.
- Quality Control: Implementing quality control measures within the ERP system ensures that products meet industry standards and customer expectations. This module helps in tracking defects and implementing corrective actions promptly.
- Procurement: The procurement module streamlines the purchasing process by automating supplier interactions, managing purchase orders, and ensuring that materials are sourced efficiently.
- Human Resources Management: ERP systems also incorporate HR functionalities that manage labor allocation, workforce scheduling, and employee performance, which are essential for maintaining a productive manufacturing environment.
The benefits of integrating ERP into production processes are manifold and significantly impact the overall success of manufacturing operations. By adopting ERP systems, companies can achieve enhanced visibility across all production stages, leading to better coordination and communication among teams. Furthermore, the automation of routine tasks reduces the risk of human error and frees up valuable resources for strategic initiatives.
“ERP systems empower organizations to make data-driven decisions that enhance operational efficiency and responsiveness.”
In addition, ERP solutions often lead to cost reductions by optimizing resource allocation and minimizing waste. For example, a manufacturer that implements an ERP system can reduce excess inventory costs by accurately predicting material needs, thus ensuring that only necessary supplies are ordered. This approach not only enhances profitability but also supports sustainable practices within the industry.
Implementation of ERP in Production
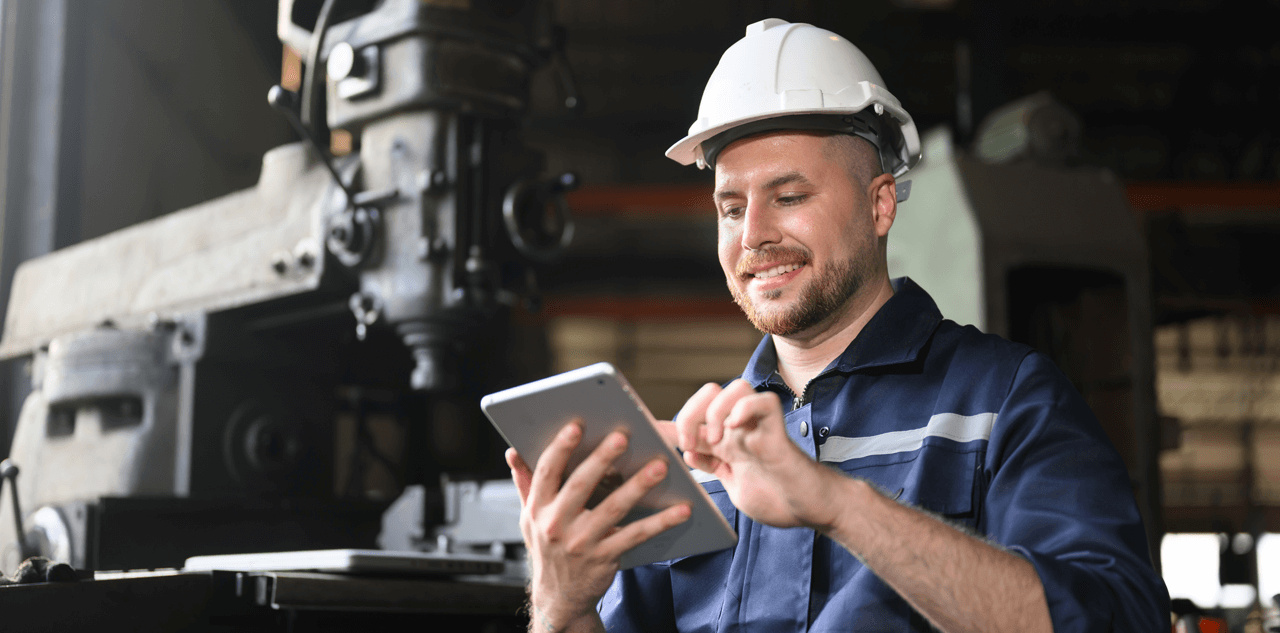
Implementing an Enterprise Resource Planning (ERP) system in a production environment is a strategic move aimed at enhancing operational efficiency and achieving better resource management. A well-executed implementation can significantly streamline processes, reduce costs, and improve overall productivity.The steps involved in implementing an ERP system in a production environment include careful planning, system selection, data migration, training, and continuous support.
Each step is crucial in ensuring that the ERP system aligns with the specific needs of the production operations.
For organizations aiming to streamline operations, the baan erp system offers an effective platform to enhance productivity. This ERP solution is designed to meet the unique needs of different industries, ensuring that businesses can adapt quickly to market changes while maintaining efficiency and control over their resources.
Steps in Implementing ERP in Production
The implementation process of an ERP system in production can be broken down into several key phases, each requiring attention to detail and a strategic approach. These phases include:
- Needs Assessment: Conduct an analysis to understand the specific requirements of the production processes and identify areas for improvement.
- System Selection: Evaluate and select an ERP solution that best fits the operational needs, considering factors like scalability, usability, and cost.
- Project Planning: Develop a comprehensive implementation plan outlining timelines, resources, and responsibilities.
- Data Migration: Transfer existing data into the new ERP system, ensuring accuracy and integrity of the information.
- Training: Provide extensive training to employees on the new system to facilitate smooth adoption and minimize disruptions.
- Testing: Conduct thorough testing of the system to identify and resolve any issues before going live.
- Go Live: Launch the ERP system and monitor its performance closely, addressing any immediate challenges as they arise.
- Continuous Improvement: Regularly review and optimize the ERP system and its usage, ensuring it evolves with the changing needs of the production environment.
Successful ERP Implementation Examples, Erp productie
Various industries have experienced transformative benefits from successful ERP implementations, serving as benchmarks for best practices. Some notable examples include:
- Manufacturing Sector: Siemens AG implemented an ERP system that integrated its production planning and inventory management, leading to enhanced operational visibility and a reported 30% reduction in inventory costs.
- Automotive Industry: Toyota utilized an ERP solution to streamline its supply chain operations, resulting in faster production cycles and improved quality control.
- Pharmaceuticals: Pfizer adopted an ERP system that improved compliance and traceability in its manufacturing processes, significantly reducing time-to-market for new products.
Common Challenges and Proposed Solutions
Despite the advantages, organizations often encounter challenges during ERP implementation. Recognizing these challenges and addressing them proactively is vital for success. Common issues include:
- Resistance to Change: Employees may be reluctant to adopt new processes. Solution: Engage staff throughout the project, encouraging feedback and emphasizing the benefits of the new system.
- Data Quality Issues: Inaccurate or incomplete data can hinder the implementation. Solution: Conduct thorough data cleansing and validation before migration.
- Insufficient Training: Lack of training can lead to underutilization of the system. Solution: Develop comprehensive training programs and provide ongoing support to enhance user competency.
- Budget Overruns: Unexpected costs can jeopardize the project. Solution: Set a realistic budget with contingency plans for potential overruns.
The successful implementation of an ERP system requires not just technology, but an organizational commitment to change and adaptation.
SAP ERP 6.0 is a robust solution that enhances business processes through its comprehensive features. Companies seeking to optimize their resource management can greatly benefit from sap erp 6.0 , which provides tools for better data management and decision-making. Its integration capabilities also allow for seamless collaboration across various departments, making it an invaluable asset for modern enterprises.
ERP Production Features: Erp Productie
Enterprise Resource Planning (ERP) systems designed for production management encompass a variety of features that significantly enhance operational efficiency and decision-making processes. These systems integrate various functions within manufacturing, including inventory management, supply chain coordination, and production scheduling, to optimize performance across the board. By leveraging these advanced tools, organizations can not only streamline their workflows but also adapt swiftly to changing market demands.Key features of ERP systems tailored for production management include modules for inventory control, production planning, quality management, and reporting analytics.
These components work cohesively to ensure that all aspects of the manufacturing process are aligned, thus facilitating a more agile response to production challenges.
Comparison of ERP Software Solutions for Manufacturing Firms
When selecting an ERP solution for manufacturing processes, it is essential to evaluate the different software available in the market. Each system offers unique functionalities that cater to diverse production needs. Below is a comparison of notable ERP solutions:
- SAP S/4HANA: Renowned for its robust integration capabilities, SAP S/4HANA offers real-time analytics and insights that empower manufacturers to optimize their processes. Its advanced planning features help in predictive maintenance and resource allocation.
- Oracle NetSuite: A cloud-based ERP solution that provides comprehensive financial and operational management tools. NetSuite is ideal for growing manufacturing firms that require scalability and flexibility in their operations.
- Microsoft Dynamics 365: This solution combines ERP and Customer Relationship Management (CRM) functionalities. It offers tailored modules for manufacturing that support production scheduling, inventory management, and quality assurance.
- Infor CloudSuite Industrial: Designed specifically for manufacturing, Infor CloudSuite emphasizes industry-specific functionality, providing tools for planning, production, and performance management. It includes advanced analytics to boost operational efficiency.
The choice of ERP software should align with the specific operational needs and strategic goals of the manufacturing firm. It is crucial to conduct a thorough analysis of the features, scalability, and user-friendliness of each solution before implementation.
Role of Real-Time Data in Enhancing Production Efficiency
Real-time data plays a pivotal role in enhancing production efficiency within ERP systems. The ability to access up-to-the-minute information helps manufacturers make informed decisions that can lead to significant improvements in operational workflows. For example, real-time monitoring of production lines allows for immediate identification of bottlenecks, enabling swift corrective actions.The advantages of integrating real-time data include:
- Improved Decision Making: Managers can analyze current production metrics and adjust strategies on the fly, optimizing resource allocation and reducing downtime.
- Enhanced Collaboration: Real-time data fosters better communication among different departments, such as sales and production, ensuring that all teams are aligned and informed about supply levels and production schedules.
- Increased Productivity: Continuous monitoring of processes allows for the identification of inefficiencies, ultimately leading to streamlined operations and enhanced output.
- Proactive Maintenance: Utilizing real-time data for equipment monitoring enables predictive maintenance strategies, which can reduce the frequency of breakdowns and extend the lifecycle of machinery.
In summary, the implementation of ERP systems equipped with real-time data capabilities can transform the landscape of production management, leading to improved efficiency, reduced costs, and enhanced competitiveness in the manufacturing sector.
Future Trends in ERP Production
As the manufacturing landscape continues to evolve, the integration of advanced technologies into Enterprise Resource Planning (ERP) systems is becoming increasingly crucial. The future of ERP in production is expected to be shaped by several emerging trends and innovations, all aiming to enhance efficiency, responsiveness, and overall operational excellence. This segment explores these trends and anticipates how they will influence the manufacturing sector.
Emerging Trends and Technologies in ERP
The convergence of new technologies with ERP systems will redefine how manufacturing organizations operate. Key trends include the adoption of cloud computing, which facilitates greater scalability and accessibility of ERP solutions, and the integration of the Internet of Things (IoT), enabling real-time data collection from production equipment.The following technologies are pivotal in transforming ERP systems in manufacturing:
- Artificial Intelligence (AI): AI enhances decision-making processes within ERP systems by providing intelligent data analysis, predictive analytics, and machine learning capabilities.
- Automation: Automation streamlines manufacturing processes, reduces human error, and increases production speed. This trend is closely integrated with ERP functionalities to coordinate various automated systems.
- Blockchain: The implementation of blockchain technology enhances data security, improves traceability, and builds trust in supply chain transactions.
- Augmented Reality (AR): AR provides immersive training experiences and real-time support for production workers, which can be integrated with ERP for improved operational efficiency.
Predictions on ERP System Evolution
The evolution of ERP systems in the manufacturing sector is poised to be influenced by the increasing demand for real-time data analytics and the need for greater flexibility in operations. Predictions indicate that ERP systems will become more user-friendly, allowing non-technical personnel to leverage their capabilities effectively, thus democratizing data access.Key predictions regarding the future of ERP systems include:
- The shift towards modular ERP solutions, enabling companies to implement specific functionalities as needed rather than undergoing a complete system overhaul.
- The growing importance of data-driven decision-making, which will necessitate advanced analytics tools being embedded directly within ERP interfaces.
- Increased focus on customization and personalization of ERP solutions to fit unique business processes and industry requirements.
Impact of AI and Automation on ERP Functionalities
The incorporation of AI and automation into ERP systems is expected to revolutionize production capabilities, leading to smarter and more efficient operations. AI technologies can enhance ERP functionalities by automating routine tasks, allowing organizations to focus on strategic decision-making and innovation.The expected impacts include:
- Enhanced Forecasting: AI can analyze historical data to provide accurate demand forecasts, helping manufacturers optimize inventory levels and production schedules.
- Predictive Maintenance: Automation combined with AI can predict equipment failures before they occur, thus minimizing downtime and maintenance costs.
- Improved Resource Allocation: Automated systems can analyze production workflows and resource usage, allowing for better allocation of materials, labor, and equipment.
“The integration of AI and automation into ERP systems is not just a trend; it is a necessity for manufacturers aiming to remain competitive in an increasingly complex market.”